Unlocking Precision: The Ultimate Guide to Tungsten Carbide Cutting Wheels
Unlocking Precision: The Ultimate Guide to Tungsten Carbide Cutting Wheels
Introduction to Tungsten Carbide Cutting Wheels
In the world of precision cutting, tungsten carbide cutting wheels stand out as an essential tool for professionals and hobbyists alike. Their durability, strength, and versatility make them the preferred choice for a wide range of applications, from metalworking to construction. At Dongcheng, we are committed to providing high-quality cutting solutions that enhance productivity and ensure superior results.
What is Tungsten Carbide?
Tungsten carbide is a compound made from tungsten and carbon. This material is renowned for its exceptional hardness, making it significantly tougher than standard steel. This hardness allows tungsten carbide cutting wheels to maintain their edge longer, providing cleaner cuts and reducing the frequency of replacements.
Key Properties of Tungsten Carbide:
High Wear Resistance: Tungsten carbide can withstand extreme conditions, making it ideal for heavy-duty cutting tasks.
Heat Resistance: It retains its hardness even at elevated temperatures, ensuring consistent performance.
Corrosion Resistance: Tungsten carbide is less prone to rust and corrosion, enhancing its longevity.
Types of Tungsten Carbide Cutting Wheels
At Dongcheng, we offer a variety of tungsten carbide cutting wheels tailored to specific applications. Understanding these types can help users select the right wheel for their needs.
1. Standard Cutting Wheels
These are the most common types, designed for general cutting applications. They are perfect for slicing through materials such as:
Metal
Plastic
Wood
2. Specialty Cutting Wheels
These wheels are engineered for specific tasks, such as:
Tile Cutting Wheels: Designed for precision cutting of ceramic and porcelain tiles.
Glass Cutting Wheels: Feature a fine edge for accurate cuts on glass surfaces.
3. Abrasive Cutting Wheels
These wheels combine tungsten carbide with other materials to enhance cutting efficiency. They excel in applications requiring:
High-Speed Cutting
Heavy Material Removal
Applications of Tungsten Carbide Cutting Wheels
The versatility of tungsten carbide cutting wheels allows them to be employed across various industries. Here are some prominent applications:
1. Metal Fabrication
In metalworking, tungsten carbide cutting wheels are indispensable. They are used for:
Cutting Steel Sheets
Trimming Metal Tubing
Creating Complex Shapes
2. Construction
Construction professionals rely on these wheels for:
Concrete Cutting: Ideal for creating clean edges in concrete structures.
Masonry Work: Efficiently cuts through bricks and stones.
3. Automotive Industry
In the automotive sector, tungsten carbide cutting wheels are utilized for:
Engine Block Machining
Brake Pad Manufacturing
4. Woodworking
Woodworkers appreciate the precision of tungsten carbide cutting wheels for:
Trimming and Shaping
Creating Decorative Edges
Choosing the Right Tungsten Carbide Cutting Wheel
Selecting the appropriate cutting wheel is crucial for achieving optimal results. Here are essential factors to consider:
1. Material Compatibility
Always match the cutting wheel with the material you intend to cut. For instance, using a tile cutting wheel on metal can lead to poor performance and damage.
2. Wheel Diameter and Thickness
The diameter and thickness of the wheel affect its cutting speed and depth. Thicker wheels are ideal for heavy-duty tasks, while thinner wheels provide precision for detailed work.
3. Arbor Size
Ensure that the arbor size of the cutting wheel matches your tool. A proper fit is vital for safety and effectiveness.
4. RPM Rating
Check the RPM rating of the cutting wheel. It should align with the specifications of your cutting tool to avoid accidents and ensure optimal performance.
Safety Tips for Using Tungsten Carbide Cutting Wheels
Safety should always be a priority when using cutting tools. Here are some essential tips to follow:
1. Wear Protective Gear
Always wear appropriate safety gear, including goggles, gloves, and ear protection, to safeguard against debris and noise.
2. Inspect the Wheel
Before use, inspect the cutting wheel for any signs of damage or wear. Do not use a damaged wheel, as it can shatter during operation.
3. Secure Your Workpiece
Ensure that the material you are cutting is securely clamped to prevent movement during cutting, which can lead to accidents.
4. Follow Operating Guidelines
Adhere to the manufacturer’s guidelines for operating speed and technique to maximize safety and effectiveness.
Maintaining Tungsten Carbide Cutting Wheels
Proper maintenance can significantly extend the lifespan of tungsten carbide cutting wheels. Here are some maintenance tips:
1. Clean After Use
Remove any debris or residue from the cutting wheel after each use. This will prevent buildup that can affect performance.
2. Store Properly
Store cutting wheels in a dry, cool place away from direct sunlight to prevent deterioration.
3. Regularly Inspect for Wear
Frequent inspections can help identify wear and tear early, allowing for timely replacements.
Conclusion
Tungsten carbide cutting wheels are essential tools that offer unmatched precision, durability, and versatility. At Dongcheng, we understand the importance of high-quality cutting solutions, and we are dedicated to providing cutting wheels that meet the diverse needs of our customers. Whether you are in metal fabrication, construction, or woodworking, choosing the right tungsten carbide cutting wheel can significantly enhance your efficiency and results. By following our guidelines on selection, safety, and maintenance, you can unlock the full potential of your cutting tools and achieve outstanding outcomes in your projects.
Explore our extensive range of tungsten carbide cutting wheels at Dongcheng, and experience the difference in quality and performance that sets us apart in the industry.
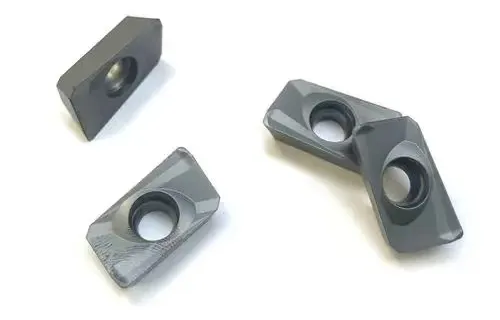