How to Choose the Right Tungsten Carbide Cutting Wheel for Your Needs
How to Choose the Right Tungsten Carbide Cutting Wheel for Your Needs
Choosing the right tungsten carbide cutting wheel is pivotal for achieving optimal results in various cutting applications. With the market flooded with options, it can be daunting to select the perfect wheel for your specific requirements. This guide aims to illuminate the critical factors to consider when making your choice, ensuring that you invest wisely and effectively. At Dongcheng, we understand the importance of precision tools, and we are committed to helping you make informed decisions.
Understanding Tungsten Carbide Cutting Wheels
Tungsten carbide cutting wheels are designed for precision cutting in a variety of materials, including metal, wood, and ceramics. The unique properties of tungsten carbide make it one of the hardest materials available, providing durability and longevity in cutting applications. Before selecting a cutting wheel, it is essential to understand the following aspects:
1. Material Compatibility
When choosing a cutting wheel, the first consideration should be the material you intend to cut. Different materials require different types of cutting wheels. For example:
Metal: For cutting metals, look for wheels specifically designed for ferrous and non-ferrous materials. Tungsten carbide wheels excel in cutting stainless steel, aluminum, and other alloys.
Wood: If your project involves wood, ensure the wheel is designed for wood cutting. Tungsten carbide wheels with a tooth design are ideal for this purpose.
Ceramics: When cutting ceramics or hard tiles, a specialized wheel with a fine grit will provide the best results.
2. Wheel Size and Thickness
The size and thickness of the cutting wheel are crucial for achieving the desired cut. Consider the following:
Diameter: The diameter of the wheel affects its cutting depth and speed. Larger wheels can cut deeper but may require more power.
Thickness: Thinner wheels are ideal for making precise cuts and minimizing material loss, while thicker wheels provide more stability and durability for heavy-duty applications.
3. Grit and Bond Type
The grit of a cutting wheel refers to the size of the abrasive particles. A finer grit is suitable for smoother finishes, while a coarser grit is better for aggressive cutting. Additionally, the bond type affects the wheel's performance:
Resin Bond: Ideal for general-purpose cutting, providing a good balance of durability and cutting speed.
Metal Bond: Best for heavy-duty applications, offering exceptional durability and longevity.
4. RPM Rating
Every cutting wheel comes with a maximum RPM (Revolutions Per Minute) rating. It is crucial to choose a wheel that matches your tool's RPM to prevent accidents and ensure optimal performance. Always check the specifications of your cutting tool to ensure compatibility with the selected wheel.
5. Application-Specific Features
Certain cutting wheels come with application-specific features that enhance their performance. For example:
Turbo Segmented Design: Ideal for fast cutting and reducing friction, making it suitable for masonry and concrete.
Diamond Coating: Provides superior cutting performance on hard materials like granite and porcelain.
Choosing the Right Cutting Wheel for Your Needs
To select the right tungsten carbide cutting wheel, follow these steps:
Step 1: Identify Your Project Requirements
Before making a purchase, take time to outline your project requirements. Consider the material type, desired finish, and the nature of the cuts you need to make.
Step 2: Consult Product Specifications
Once you have a clear understanding of your needs, consult the product specifications of available cutting wheels. Look for detailed descriptions from reputable brands like Dongcheng, which provide insights into the wheel's capabilities.
Step 3: Test Different Wheels
If possible, test different cutting wheels on sample materials. This hands-on approach will give you a better sense of how each wheel performs under practical conditions.
Step 4: Evaluate Cost vs. Value
While it may be tempting to opt for the cheapest option, consider the long-term value of the cutting wheel. Investing in a high-quality wheel from a trusted brand like Dongcheng can lead to better performance, durability, and overall cost-effectiveness.
Maintaining Your Tungsten Carbide Cutting Wheels
Proper maintenance is essential for maximizing the lifespan and performance of your tungsten carbide cutting wheels. Here are some tips:
1. Clean After Use
After each use, clean your cutting wheel to remove any debris or residue. This will prevent build-up that can affect performance.
2. Store Properly
Store your cutting wheels in a dry, cool place. Avoid exposing them to moisture, as this can lead to corrosion and degradation.
3. Inspect Regularly
Regularly inspect your cutting wheels for signs of wear and tear. Replace any wheels that show significant damage or reduced performance to ensure safety and efficiency.
Conclusion
Choosing the right tungsten carbide cutting wheel is a crucial step in achieving the best results in your cutting projects. By considering material compatibility, wheel size, grit, RPM rating, and application-specific features, you can make an informed decision that meets your needs. At Dongcheng, we pride ourselves on offering high-quality cutting tools that cater to a wide range of applications. By following the guidelines outlined in this article, you can ensure that you select the perfect cutting wheel for your projects, allowing you to work efficiently and effectively.
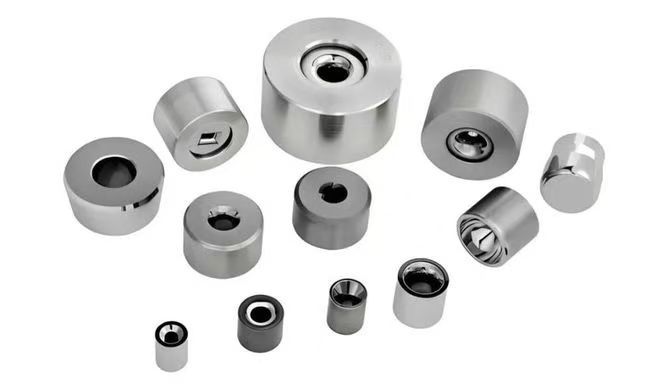